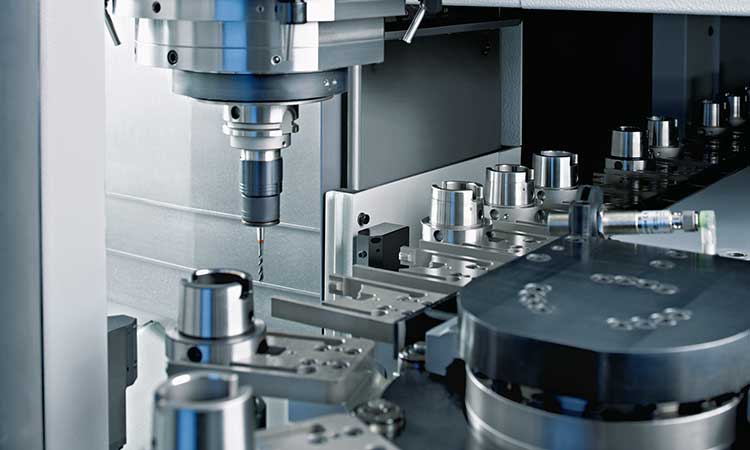
Automotive is among of the biggest users of die-cast components in Malaysia, with manufacturers relying on the process to produce lightweight and durable components. Die-cast parts made of zinc and aluminum are extensively used in automobile production due to their strength in addition to their low weight and resistant to rust. Transmission housings, engine components as well as brackets and structural parts are among die-cast components that contribute to the overall performance and efficiency of contemporary automobiles. With Malaysia being the home of some major automotive manufacturers and suppliers, the local die-casting sector has benefited from strong demand for high-quality, precision-engineered metal components. Many die-casting companies have invested in advanced machines and automated equipment to meet the high standards for quality demanded by the automotive sector. As electric vehicles gain popularity, the industry is also adapting to produce special die-cast parts that include battery casings and motor housings and light components for structural use.
Die casting also plays a significant role for the electronics and telecommunications sectors in Malaysia in which precision and reliability are essential. The nation is a leading exporter of electronic parts, providing global companies with top-quality heat sinks, metal enclosures and connectors. Die casting's ability to make complex forms with tight tolerances makes it ideal for manufacturing these parts, which ensures they are compatible with a variety of electronic devices. Many Malaysian die-casting firms work with tech companies to create specific solutions to smartphones, laptops, data centers, as well as telecommunications equipment. Due to the continuing growth of the electronic economy, demand for high-end die-cast parts will likely to increase. Companies are focusing on increasing the electrical shielding, thermal conductivity, and lightweight properties in order to increase the efficiency of electronic components. Automation and advanced manufacturing methods can further improve effectiveness in the manufacture of high-precision metal parts.
Sustainability has been a key focus for Malaysia's die-casting industry, with companies actively implementing environmentally friendly manufacturing practices. Recycling and reusing metals, specifically zinc and aluminum, are now common practice in die casting, reducing the amount of waste produced and preserving resources. A lot of manufacturers have adopted the most energy efficient melting and casting techniques to reduce carbon emissions as well as general energy use. The shift toward sustainable manufacturing has prompted the industry to explore more environmentally friendly casting methods, such as low-pressure die casting and gravity die casting that produce high-quality parts with minimal production waste. The coatings and treatments used to enhance the durability and corrosion resistance of die-cast components are being designed using green components. With industries around the world pushing for greener supply chains, Malaysian die-casting firms are establishing themselves as leaders in the field of sustainable metal casting ensuring long-term competitiveness in the global market. To get supplementary details please visit Senadiecasting
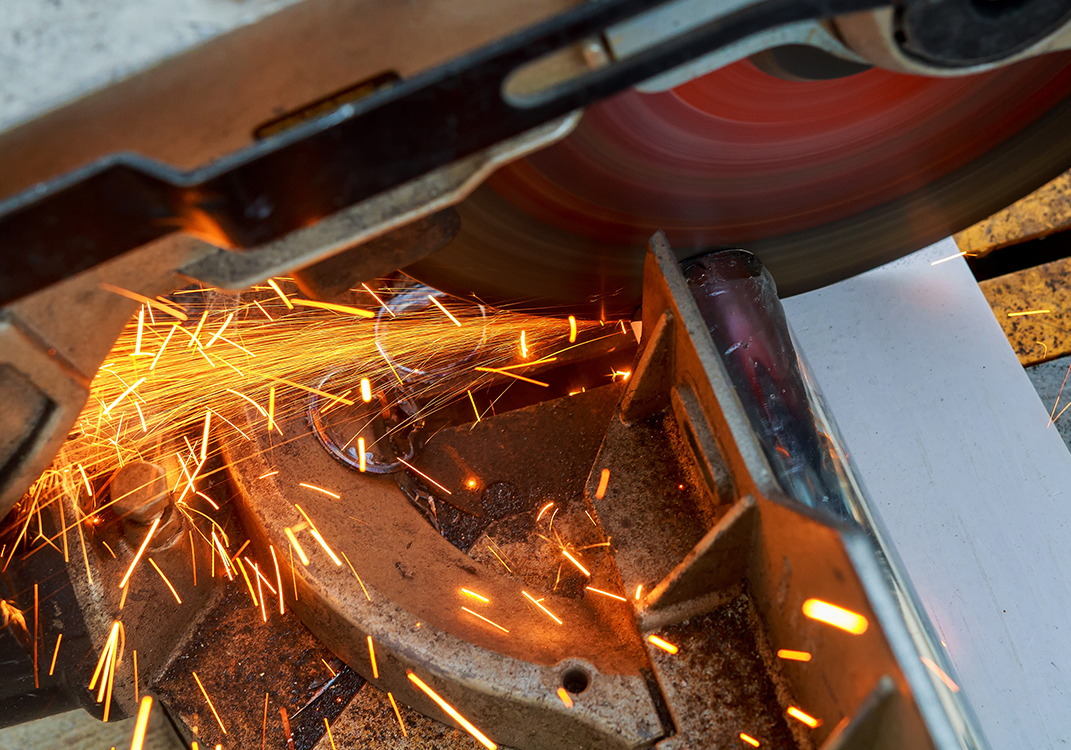
The technological advancements in die casting have transformed the manufacturing industry in Malaysia, and allowing companies to produce more complex and high-performance components. Technologies like computer-aided design , 3D printing for mold prototyping, and real-time monitoring systems are improving precision and decreasing production mistakes. Automation and robotics are also becoming integrated into die-casting procedures to improve production efficiency, cut down on labor expenses, and ensure consistent high-quality. This technology allows Malaysian companies that manufacture dies to compete with international manufacturers by offering superior products with less time to lead. Utilizing Industry 4.0 technologies, such as the Internet of Things and artificial intelligence , further improves production efficiency and predictive maintenance. With the adoption of these advanced technologies the die-casting industry in Malaysia is strengthening its position as a leading manufacturing center which is capable of meeting the changing demands of international markets.
As we look to the future, Malaysia's die-casting industry will likely to witness significant expansion, driven by sustainability, innovation increasing demand for precision metal components. Leaders from the industry and government are working together to enhance the research and development of initiatives that encourage the implementation of advanced materials and new casting methods. Training programs for workers are in place to provide professionals with the necessary skills in operating modern die-casting equipment as well as automation equipment. In a time when industries like electric vehicles, renewable energy and smart technology continue to grow, Malaysia's die-casting sector is well placed to satisfy the growing demand for high-performance metal parts. Malaysia's robust industrial infrastructure and its dedication to sustainable development and technological innovation will ensure that Malaysia continues to be a leading participant in the worldwide die-casting marketplace. Through continuous improvement and strategic investments, this sector is expected to continue driving the economy and maintain its standing as a source of high-end precision manufacturing.